Improving efficiency: the best practice of flat wire drawing and polishing machine
- 2024-11-18 14:44:41
- 0
- Suzhou su men yi Jia numerical control technology co., ltd
Flat wire drawing and polishing machine is a key equipment for metal surface treatment, widely used in wire drawing and polishing processes of metals such as stainless steel, aluminum alloy, copper alloy, etc. It is crucial to adopt some best practices in order to maximize the production efficiency of the equipment and improve processing quality. Here are several key points to improve the efficiency of flat wire drawing and polishing machines:
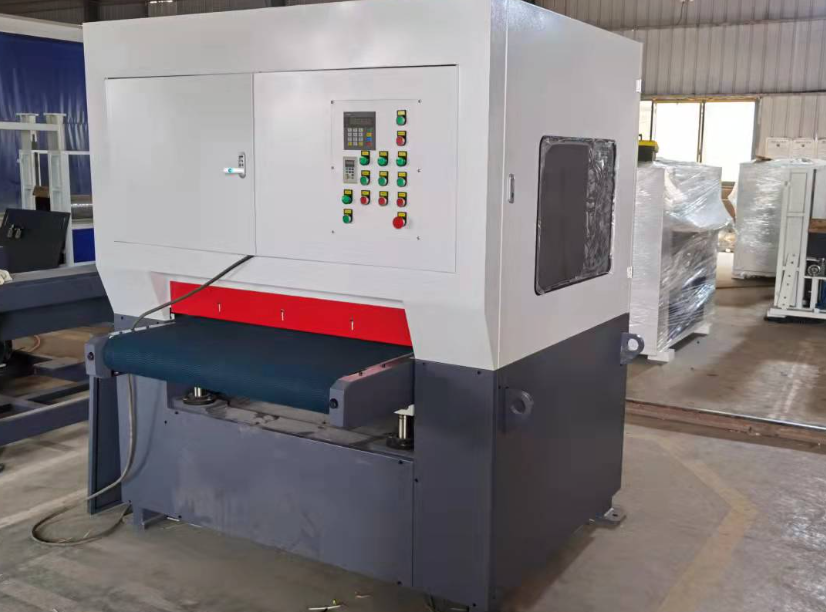
1. Set up the device correctly
Before starting the operation, ensure that the machine's settings are correct. Choosing the appropriate sand belt width, speed, and abrasive is crucial. Different metal materials require different sand belts and abrasives. Using unsuitable abrasives not only affects the surface effect, but also leads to rapid equipment wear, thereby reducing efficiency. Regularly inspecting and calibrating equipment to ensure it is in optimal working condition can significantly improve processing efficiency.
2. Regular maintenance
Regular maintenance is the key to maintaining efficient operation of equipment. After each use, the equipment should be cleaned and the wear of components such as sanding belts, abrasives, and pressure systems should be checked. Keeping the equipment in good condition can reduce the occurrence of failures, avoid downtime, thereby reducing production interruptions and improving work efficiency. Especially in high-intensity production environments, timely replacement of worn parts can also avoid equipment failures and ensure stable operation.
3. Optimize the production process
Improving production efficiency not only depends on the performance of equipment, but also on a reasonable production process. Efficiency can be improved by planning the work area reasonably, reducing the handling time of workpieces, and optimizing the operation process. For example, an automatic feeding system can reduce manual intervention, achieve automated production, and thus improve production efficiency. In addition, preparing workpieces and materials in advance to avoid frequent downtime and equipment adjustments during the production process can greatly reduce equipment idle time.
4. Operator training
The skills of operators directly affect the operational efficiency and processing quality of equipment. Providing professional training for operators, enabling them to proficiently master machine operation skills and common problem handling methods, can effectively reduce operational errors and improve overall production efficiency. Understanding how to adjust machine parameters correctly and determine whether the equipment is working properly is the key to ensuring efficient operation.
5. Reasonably arrange production plans
A reasonable production plan can effectively improve the utilization rate of machines, avoid overloading or production bottlenecks. Adjust the production pace according to order requirements and production volume to ensure that the equipment operates in an efficient working state. In addition, avoid running the equipment under overload conditions for a long time to avoid affecting the machine's lifespan and production efficiency.
Through the above best practices, the work efficiency of the flat wire drawing polishing machine can be significantly improved, production costs can be reduced, and product quality can be ensured. Implementing these measures can not only extend the service life of equipment, but also improve overall production efficiency and bring higher competitiveness to enterprises.